损伤事项 |
损伤状态 |
原因 |
对策 |
图样 |
表面剥落 |
沟道单侧全周表面剥落 |
安装不良或因轴膨胀造成异常轴向负荷 |
游隙与自由侧轴承外轮的配合相符 |
|
沟道内钢球间距表面剥落 |
安装时的冲击负荷 |
小心安装 |
|
运转停止时的锈 |
长期不运转时需防锈处理 |
|
沟道面、钢球面的早期表面剥落 (图1) |
负荷过大 |
适当的配合 |
|
游隙过小 |
适当的游隙 |
润滑不良 |
适当的润滑剂和量 |
安装不良 |
重新查看轴、支架的精度、安装方法 |
锈 |
保管、使用注意 |
相对于沟道倾斜的表面剥落 (图2) |
安装不良 |
安装作业注意 |
|
轴的弯曲 |
选用游隙大的轴承 |
轴、支架的精度不良 |
轴、支架的垂直度修整 |
沟道对称位置的表面剥落 |
支架的精度不良 |
支架内径面的精度修整 |
|
压痕 |
沟道内有钢球间距的压痕、打痕 (图3) |
安装时落下时的冲击负荷 |
使用注意 |
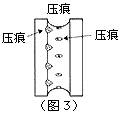 |
静止中或低速回转中的负荷过大 |
重新查看静止负荷 |
沟道、钢球面有压痕 |
砂、金属粉等的侵入 |
轴、支架的清洗,重新查看密封装置 |
|
擦伤、烧伤 |
沟道、钢球面的变色、软化溶粘 (图4) |
负荷过大 |
适当的配合 |
|
游隙过小 |
适当的游隙 |
润滑不良 |
适当的润滑剂和量 |
安装不良 |
安装方法和有关部件的复查 |
电蚀 |
沟道、钢球面有洗衣服板状的电蚀 (图5) |
电流通过轴承产生的火花 |
接地线、轴承绝缘 |
|
破损 |
沟道面的破裂、缺损 (图6) |
冲击负荷过大 |
适当的负荷条件 |
|
过盈量过大 |
适当的配合 |
表面剥落或烧伤的进展 |
轴和套的修整 |
安装部的圆角大 |
把圆角修整成比轴承倒角小 |
钢球的破裂、缺损 |
冲击负荷过大 |
适当的负荷条件 |
|
运转中游隙过大 |
配合和轴承游隙复查 |
|
保持器的破损 (图7) |
力矩负荷 |
注意使用 |
|
高速及高加速度回转的冲击 |
复查回转条件 |
润滑不当 |
润滑剂、润滑方法的复查 |
异物进入 |
改善密封装置 |
粘着 |
沟道、钢球面的粘着,擦伤、烧伤 (图8) |
润滑不当(硬的油脂、量不足) |
注入适当量的柔软的油脂 |
|
开始回转时的加速度大(钢球的滑动) |
不急着加速 |
磨损 |
沟道、钢球、保持器的异常磨损 (图9) |
异物侵入 |
改善密封装置 |
|
锈 |
保管、使用注意 |
润滑不良 |
适当的润滑剂和量 |
配合面的粘着磨损,蠕变 (图10) |
过盈量不足 |
适当的配合 |
|
套筒的拼紧不足 |
适当的套筒拼紧 |
配合面的红色磨损、微振磨损(图11) |
配合面的微小间隙 |
加大过盈量 |
|
沟道有钢球间距的微振磨损,不正确的表面变形现象 |
在输送中轴承停止状态的振动 |
固定轴和支架 |
|
小振幅的摇动运动 |
使用润滑油,预压 |
|
锈、腐蚀 |
轴承内部的锈 |
保管状态不良 |
注意保管 |
|
空气中的水分造成的结露 |
注意保管 |
|
配合面的锈 (图12) |
微振磨损 |
加大过盈量 |
|
变动负荷 |
在配合面涂上油 |
“损伤”腐蚀 |
酸、碱、气体的侵入 |
密封装置的复查 |
|
润滑剂的化学作用 |
润滑剂的复查 |
|
为什么轴承会磨损坏
仅有部份的轴承在实际应用中损坏。大部份的轴承抽坏的原因很多——超出原先预估的负载,非有效的密封、过紧的配合所导致的过小轴承间隙等。这些因素中的任一因素皆有其特殊的损坏型式且会留下特殊的损坏痕迹。因此,检视损坏轴的承,在大多案例中可以发现其可能的导因,大体上来说,有三分之一的轴承损坏导因于疲劳损坏,另外的三分之一导因于润滑不良,其它的三分之一导因于污染物进入轴承或安装处理不当。 然而,这些损坏型式亦与工业别有关。例如,纸浆与造纸工业多半半是由于润滑不良或污染造成轴承的损坏而不是由于材料疲劳所致。